Originally published in the OG Directory (8/24/2021)
The varied environments and applications found in Oil and Gas can create some challenges for the real-time monitoring of toxic and combustible gases.
Here are three areas to consider when selecting gas detection equipment to keep your employees and assets safe:
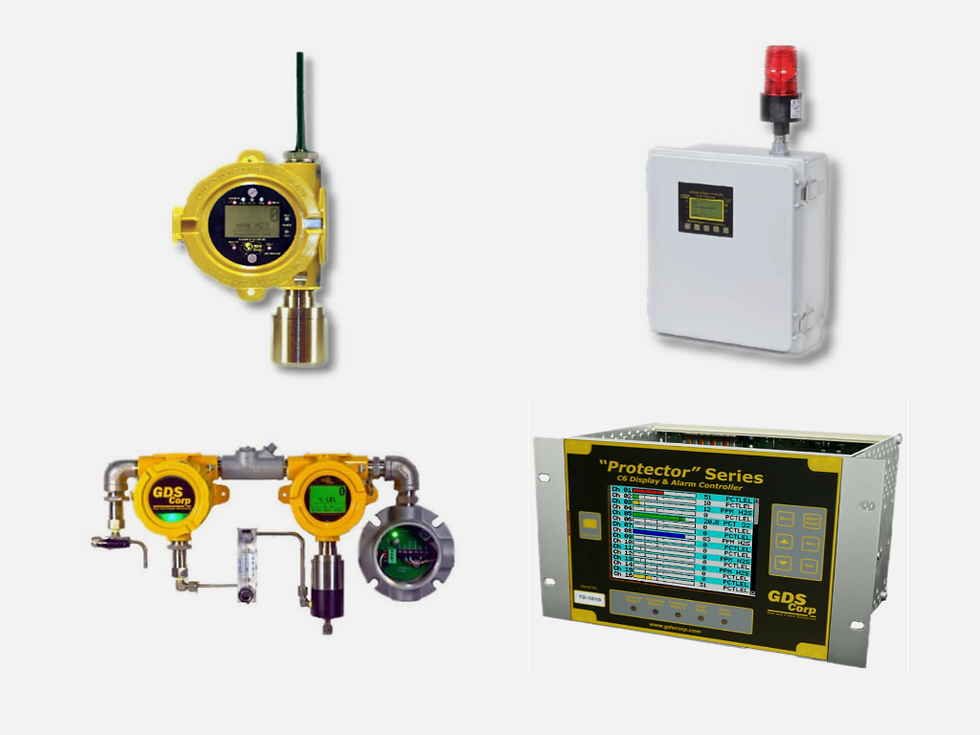
Adaptability
Physical layout of facilities and existing data systems are prime examples of the necessity for systems that are highly customizable. Class 1/Division 1 designs and wireless technologies make it possible to place sensors and controllers precisely where they are needed. Depending on the technology employed by a specific manufacturer, a wireless sensor could reach a range of 10 miles.
On the data front, look for a system that allows for multiple output protocols from the sensor so that you do not have to choose one protocol over the other if both are needed. Programmable relay outputs are also needed to provide for audible and visual alarms, where even low level gas exposure can be deadly.
Further flexibility is possible by choosing a provider with a wide array of sensor types, target gases, and available concentration sensitivities.
Smart Technology
Maintaining the inventory of sensors should be automated via Smart Sensor Technology that allows the user to easily track born-on and install dates, calibration intervals, and sensor life.
Ease of Use for Accuracy & Reliability
Design features such as magnetic switches ensure the configuration and calibration processes necessary to maintaining the system are easy to perform.
Integrity Controls is a manufacturer’s representative for gas detection solutions provider GDS Corp. Integrity also represents A-T Controls/TRIAC ball valves, Eaton Filtration, WIKA gauges, and Sofis valve interlocks/remote operators; as well as many other control/measurement manufacturers. Contact us 303.781.7098 or Derek.Johnson@Integrity-Controls.com to learn more.

Comments